In the agri-food industry, the weight displayed on the packaging must meet specific requirements (TU1, TU2, etc.) in accordance with the regulations. The final weight of a product at packing may be impacted by different factors, such as the manufacturing process, the ingredients, or the recipes. If a product does not comply with the rules (TU2 = defective product), it must be discarded. However, overdosing implies a loss of raw material. This is where process data analysis comes into play. To your scales!
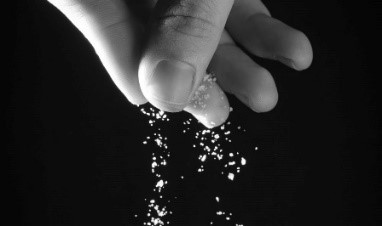
Meal preparation to the nearest gram!
Are big data and artificial intelligence relevant solutions for the agri-food industry? Not necessarily: we supported our client in collecting enough of the required data to be able to identify the most suitable solution quickly. Based on the analysis of the manufacturing process, we decided to collect the weights of all the trays passing through the line at the two key production stages: at dosing, where the quantity of each ingredient is adjusted, and at packaging, where compliance with regulations is verified. As the scales were already installed, they simply had to be adapted to collect the weights and store them in a database. This strategy is far from big data, which requires a specialised infrastructure. Here, the database is free and easily hosted on the client’s website.
In workshops with the teams involved, we defined the tools and data display requirements to improve the control of one of the processing lines. This strategy differs a lot from artificial intelligence in science fiction films: we simply converted the “common sense” of people, who understand the process, into mathematical and computing requirements.
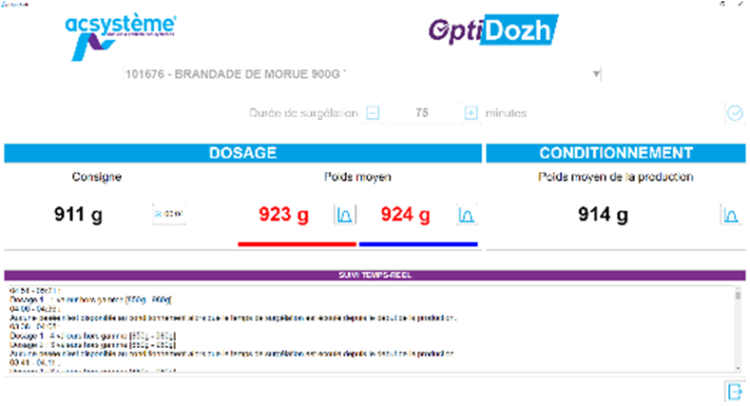
An on-line tool for the production line workers: rather than dosing based on experience, the tool calculates a target dosing weight to ensure product compliance with the regulations. The target weight is determined product by product, by means of statistical algorithms applied to production history, such as standard deviations or averages. As a result, performance no longer depends on the team’s experience: they can trust the weights recommended the software.
A tool for the managers: For department managers and job experts we also developed a product management and production analysis tool, to add new recipes, study the production results closely, monitor the gains made over time, etc. The tool helps confirm intuition by observing how the production line works, identifying improvement solutions (working methods, change of equipment, etc.), and possibly changing the parameters of the target weight calculation. The impact of these updates can then be assessed over time.
A night-time tool: production operates on average for 16 hours a day, but it is at night when everything happens whilst everyone is asleep. A third software takes advantage of the calm in the factory to wake up and study the production data for the previous day, to increase its knowledge of each recipe continually and to adjust its recommendations.
After a few months, the return on investment is obvious. We can finally adjust the dosing to the nearest gram! Deployment on other lines is in progress and other topics have been identified: data analysis at the service of industrial performance!