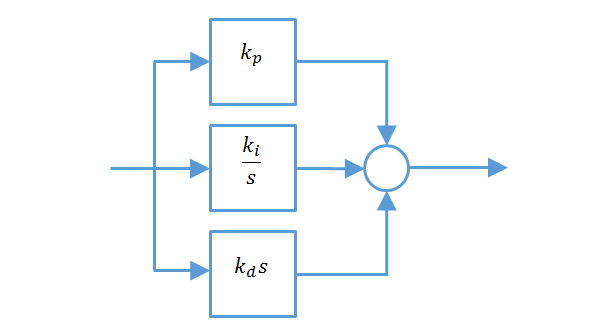
Serial or parallel PID, which structure to pick?
Introduction
Recently, one of our clients asked a relevant question: to implement my controller, should I use a serial or parallel PID structure? Indeed, during our first courses of automatic controls, the instructor presents the way of building a PID, but does not specify when you should pick one over the other.
1. Serial or parallel PID
The two structures are described by the following equations:
- serial :
Cserial(s) = k(1+1⁄(sτi) )(1+sτd)
- parallel :
Cparallel(s) = kp + ki ⁄s + kds
As you can see, they are mathematically equivalent. From a serial controller, it is always possible to switch to a parallel form, thanks to these formulas:
- kp = k(1 + τd ⁄τi )
- ki = k⁄ τi
- kd = kτd
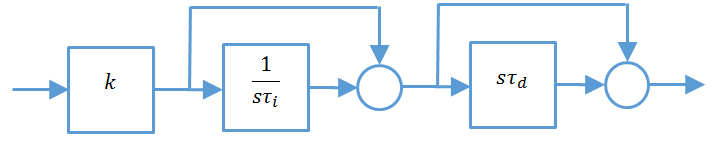
Fig 1 : serial PID
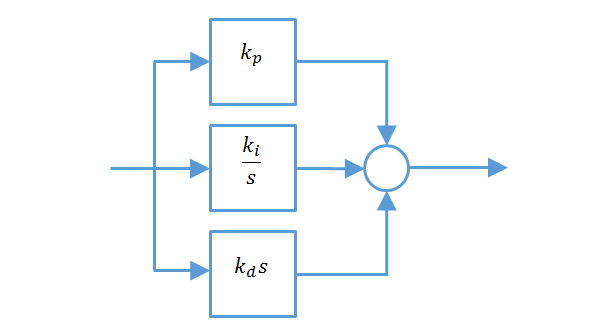
Fig 2 : parallel PID
2. A 3rd way to implement a PID
Another way to build PID exists! It is called “standard”, “mixed” or sometimes “ideal”. It is defined by the equations bellow :
Cstandard(s) = Kp(1 + 1⁄sΤi + sΤd )
This new form and a regular parallel form are a lot alike. So, transformation equations are easy to obtain :
Kp = k(1 + τd ⁄τi )
Τi = τi + τd
Τd = τdτi ⁄(τd + τi)
In the end, there are three different ways to implement PID, almost mathematically equivalent. Generally speaking (except when ki=0), there are formulas for transforming a controller from one form to another.
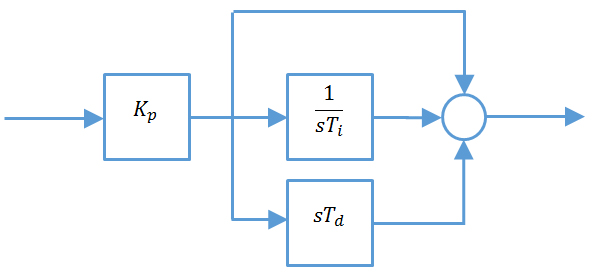
3. The main difference
The main difference between those structures is the effects of setting coefficients on the controller’s behavior. The parallel form allows for a complete decoupling of proportional, integral and derivative actions whereas with a standard structure a modification of the Kp coefficient will affect proportional, integral and derivative actions. It is the reason why people who manually set the controller rather use the parallel form.
The serial form is sometimes implemented in control automaton available on the market. There is a second way to formulate it:
Cserie(s) = (1+τ1)(1+τ2)⁄τi(1+τNs)
This formulation eases the link between time constants of the process and setting parameters of the controller, particularly with the two real zeros in the numerator.
In the industry sector, standard and parallel form are the most common. Then, with Simulink software, the “PID controller” block can be set to standard (“Ideal”) or parallel form.
Another important aspect of parallel and standard PID: they are not able to cancel the integral action. This results in the inability to turn this kind of PID into a PD controller.

3. The main difference
The main difference between those structures is the effects of setting coefficients on the controller’s behavior. The parallel form allows for a complete decoupling of proportional, integral and derivative actions whereas with a standard structure a modification of the Kp coefficient will affect proportional, integral and derivative actions. It is the reason why people who manually set the controller rather use the parallel form.
The serial form is sometimes implemented in control automaton available on the market. There is a second way to formulate it:
Cserie(s) = (1+τ1)(1+τ2)⁄τi(1+τNs)
This formulation eases the link between time constants of the process and setting parameters of the controller, particularly with the two real zeros in the numerator.
In the industry sector, standard and parallel form are the most common. Then, with Simulink software, the “PID controller” block can be set to standard (“Ideal”) or parallel form.
Another important aspect of parallel and standard PID: they are not able to cancel the integral action. This results in the inability to turn this kind of PID into a PD controller.
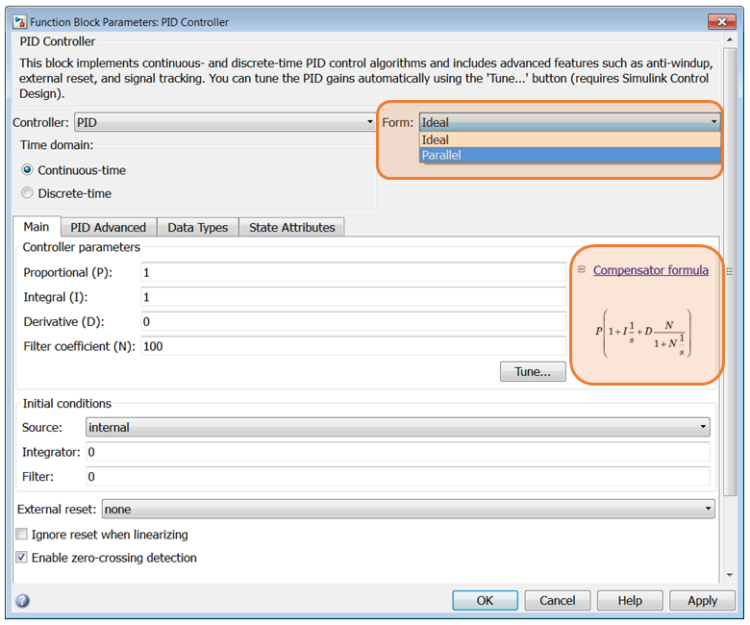
4. Conclusion
To cut a long story short, it is hard to prescribe a particular form to implement a PID controller, each has its drawbacks and advantages. The standard structure is the most widespread in the field of industry. In the end, it is important to know that the forms are quite similar and there are formulas to switch from one to another. The differences are mainly caused by the effect of setting parameters on the control loop behavior, which is essential for manual calibration.
If you are still hesitating in spite of this advice, please contact Acsystème’s advisors. They will help you analyze your needs in order to make the right choice.
References :
[1] Philippe de Larminat, Automatique appliquée, 2e édition revue et augmentée, Chapitre 2, Hermès Lavoisier, 2009.
[2] A. Besançon-Voda et S. Gentil, Régulateurs PID analogiques et numériques, Techniques de l’ingénieur, R 7 416, mars 1999.